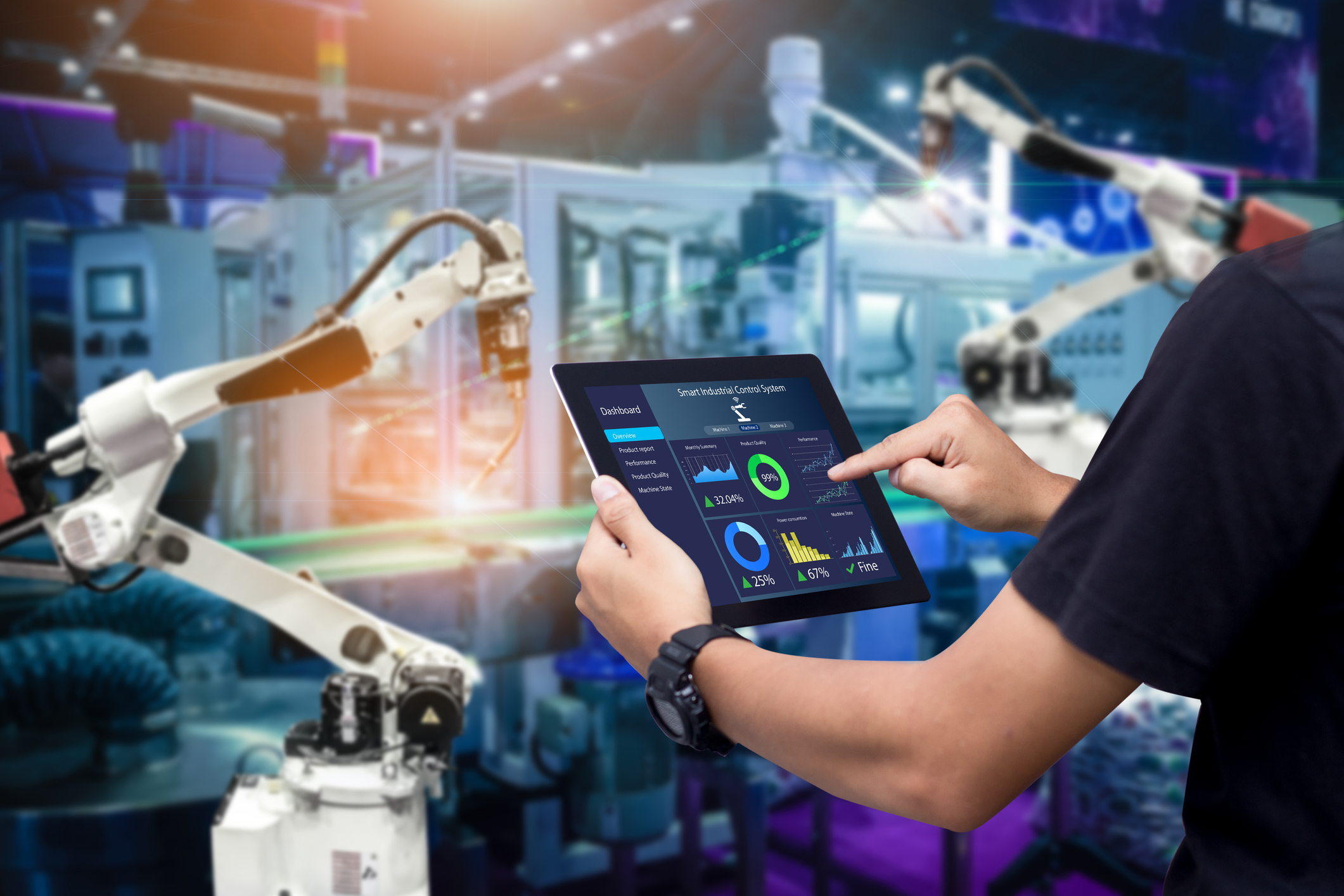
Zero Defect Manufacturing for the Medical Device Industry
Does it ever feel like the rate of defective products in today’s manufacturing environment is getting worse, despite improved quality management systems? If you think that, you may be right! Today’s manufacturing environment has an increasing emphasis on smaller batches of parts created ever more quickly, for lower costs – which has led to an increase in rates of defected parts. While these defect rates are acceptable for many consumer products, increasing rates of defective parts are unacceptable for medical manufacturers. For one, these increased rates can lead to re-work and increased costs, in an era of downward price pressure. Furthermore, the consequences of defective parts in both liability and patient outcomes are at odds with medical device manufacturer’s goals. “Zero Defect Manufacturing” addresses both of these problems, providing the right part the first time, every time.
Obviously, a completely defect-free environment isn’t achievable in reality. However, the definition of 3.4 defects/1,000,000 parts is probably as close as we can get and what “Zero Defect Manufacturing” aspires to. First created to address defects in aerospace manufacturing, Zero Defect Manufacturing has four main concepts:
1) The Definition of Quality is Conformance to Requirements
Every project at Timbercon has rigorously defined requirements – whether created by our expert design engineers, or coming from your own design teams, we will make sure that any fiber optic cable or assembly has clearly defined performance objectives that meet or exceed what is needed for the final product. One of the main sources of defective products and frustrated engineers is when specifications are “assumed” or improperly defined.
2) The System of Quality is Prevention
Many modern medical manufacturers rely less on skill and lean on inspection methods to screen out defective parts (hopefully before shipment). This is especially true for manufacturers who are new to the medical industry or used to making consumer-level products. While final inspection is important, an over-reliance on inspection to compensate for poor design or improper manufacturing techniques leads to increased costs (as failed parts are manufactured multiple times, in essence) as well as increasing defect rates, as some parts invariably slip through final inspection. Zero defect manufacturing addresses this with an emphasis on building parts properly the first time, every time.
3) The Performance Standard is Zero Defects
In an increasingly measured world, where it seems that everything has a metric, workers are under pressure to produce more parts in less time. In this environment, passing along a potentially defective part is typically less risky (for operators) than addressing potential shortcomings right away. Zero Defect Manufacturing empowers workers to produce only parts that meet the accepted performance criteria as their personal standard. This, in turn, leads to a virtuous cycle where defect rates fall, and productivity rises while manufacturing costs decrease.
4) The Measurement of Quality is the Price of Nonconformance
What this means, in plain English, is that there is a cost to producing bad parts. This cost flows through the entire manufacturing chain – from the manufacturer, all the way to the final user. When the final destination is a clinical environment, the downstream cost is even greater. Acceptance of this encourages managers at all levels to ensure that quality systems are in place to maintain extremely high levels of product quality and conformance.
These core concepts of Zero Defect Manufacturing are common practice for products in space exploration or aerospace industries. Now, this same level of quality can be available for your medical fiber optics, at a surprisingly low cost. Timbercon has decades of experience designing and manufacturing fiber optic cables and assemblies for the world’s most demanding projects. Contact us today for a free design review on a new project or quotation on an existing assembly – and see how Zero Defect Manufacturing can help ensure the highest quality and lowest cost for your medical device – because our customers (and your patients) deserve the best.